25 March 2024
Lean methodology drives continuous improvement at HSV Distribution Centres
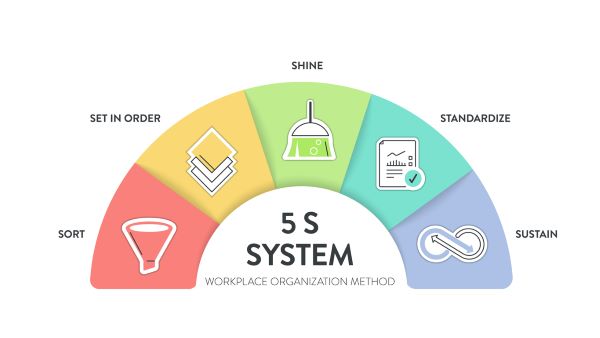
HSV’s Logistics team is introducing lean 5S methodology at the Derrimut and Dandenong South Distribution Centres to drive further improvements in its operations.
HSV Head of Distribution Centre Operations Josh Lotter says the lean methodology will help to foster a culture of continuous improvement by increasing efficiencies and improving consistency of service.
The 5S lean system originated in Japan in the 1950s with the Toyota Production System and is said to be the inspiration for the now infamous KonMari method of home organisation. The 5Ss symbolise the five steps needed to optimise efficiency as much as possible so there is no wasted effort – Sort, Straighten or Set in Order, Shine, Standardise and Sustain.
Some of the benefits of implementing 5S include increased productivity, higher quality standards, a safer work environment and improved employee satisfaction.
Josh says HSV is in the early stages of 5S implementation. The team has rolled out several initiatives as part of the ‘sort’ phase, including a new safety board (pictured).
“The green cards are used to indicate shifts without incidents, while red cards indicate those where safety concerns have arisen,” Josh says.
The goal is to drive a proactive safety culture and capture safety data to help us make more informed decisions.”
A new roster at the entry to the Derrimut Distribution Centre lets staff know where they will be working for each shift, while pigeonholes provide a home for RF (radio frequency) scanners that must be signed in and out after each use.
“Our team members can see exactly where they need to go as soon as they start their shift,” explains Josh.
“It’s part of our goal to reduce process variation. During the ‘sort’ phase of 5S we’re also making sure every piece of equipment in daily use has a home.”
The team has introduced a centralised system for everything from batteries and cleaning equipment to forklift keys and tape guns.
Josh says the 5S implementation is expected to take between six and nine months, starting with training for staff at HSV’s Distribution Centres.
As the team continues with its improvement program, HSV’s State Supply Chain (SSC) customers are reporting prompt delivery times, including to regional health services.
Goulburn Valley Health Procurement Coordinator Warren Norton says while there were teething problems in the early days of the SSC handover to HSV, deliveries are now arriving within two to three days.
“Being a regional health service that’s a great result for us,” he says.
“If we have a COVID outbreak it takes the pressure off knowing that a delivery of PPE will turn up when it’s supposed to.”
“Even when we did experience issues, communication with HSV was good and we were able to resolve them quickly.”